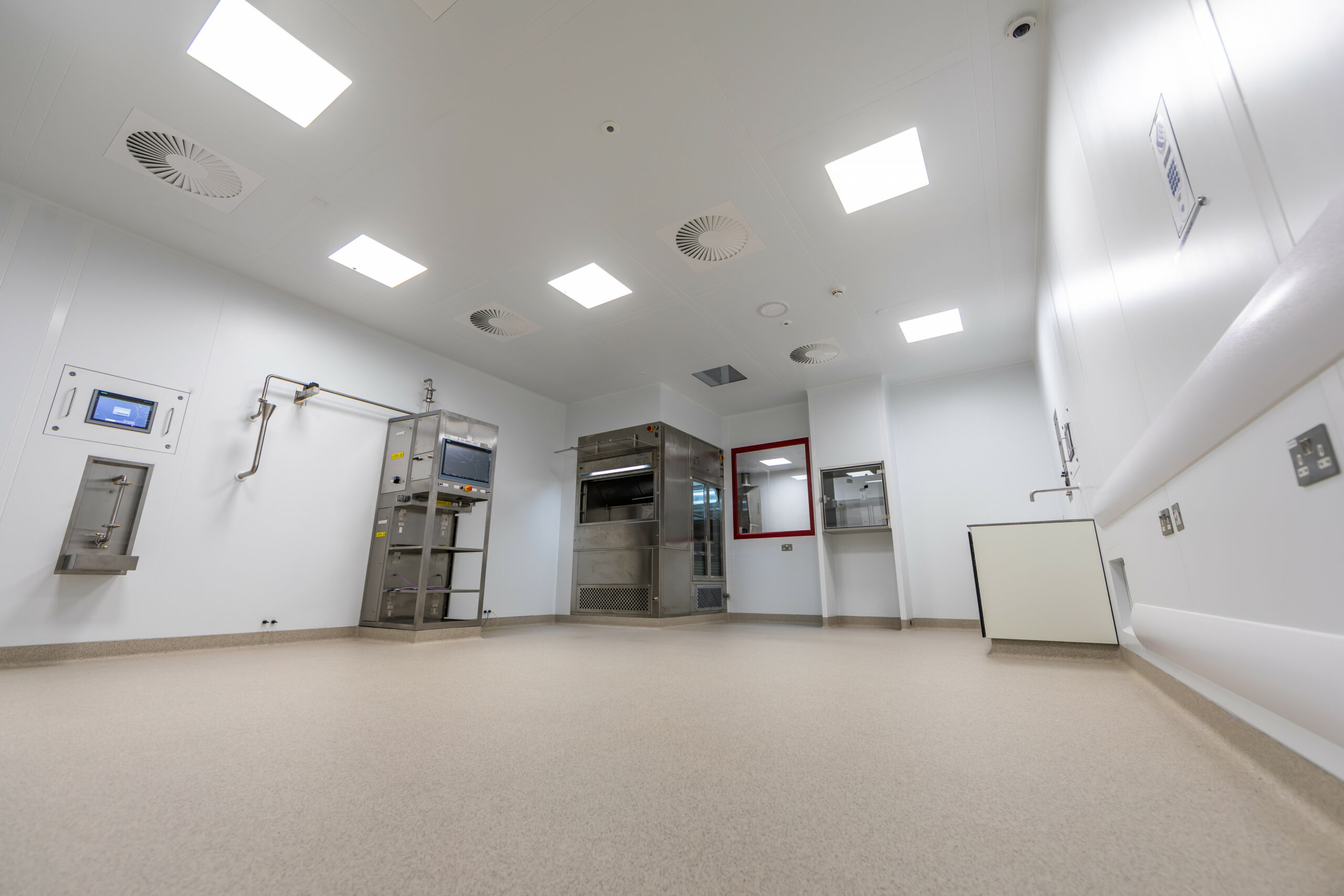
All too often Clients and Contractors take the approach that construction quality is achieved by inspecting the works after they are completed, finding the snags, defects, and non-conformances, and getting them rectified. This “process” can either be during the construction period or, in many cases, after project completion and sometimes, even when the facility is in use. Rectifying defects which come to light once a building is in use can be difficult and inconvenient. And there are classes of projects where gaining access to the operational facility goes far beyond difficult and inconvenient. Cleanrooms are one such type of project.
The primary use for cleanrooms is to limit contamination from dust, vapour, microbes, fibres, or other biological hazards. Cleanroom systems can also be used to regulate temperature, humidity, airflow, filtration, and pressure. They have complex systems to achieve these requirements which are time consuming and expensive to set up, commission and calibrate. Going back into a cleanroom facility to rectify defects would have severe consequences for the environment and consequently the processes, which are carried out in them, would have to stop. This would have enormous repercussions for the operator of the facility.
McLaughlin & Harvey are contractors who have an extensive track record in the delivery of cleanrooms. Derek Geyer, Head of Quality at McLaughlin & Harvey writes about the get it right approach, at all stages, that is required for the delivery of cleanrooms.
Q – Is planning for quality important in this field of construction?
A – No, it’s critical
When you assess the risks of getting quality wrong in this environment you cannot afford to build errors in, nor can you accept right second time. If you turn the clock back to 1987, the late quality guru Dr Joseph M. Juran penned ‘Planning for Quality’. This, as well as most of Juran’s work, focused on ‘doing it right first time’. He was very descriptive in what he meant by this, explaining that to achieve this positive outcome time and time again the following would need to exist:-
- Establish specific goals to be reached
- Establish plans for reaching these goals
- Assign clear responsibilities for meeting the goals
- Base the rewards on results achieved
A year earlier in 1986, Juran presented his Quality Trilogy model. Back then the traditional approach to quality was around control. However, those who are familiar with the trilogy today know that this is the basis for most quality management practices around the world.
The trilogy is made up of Quality Planning, Quality Control and Quality Improvement.
Most people jump to the third stage of the trilogy and look to improve the quality of how they deliver the product or service aiming to exceed customers’ expectations. However, they fail to note that without a clear plan in place you will never achieve your customer’s expectations let alone exceed them.
So, what does this have to do with the quality process in clean room construction?
The primary use for cleanrooms is to limit contamination from dust, vapour, microbes, fibres, or other biological hazards. Cleanroom systems can also be used to regulate temperature, humidity, airflow, filtration, and pressure. If errors are built into a facility like this, then the time and cost to shut an area, building or factory down, to then get back in to rectify any defects, can be huge for an organization resulting in financial and reputational damage. In addition to this, the risk of any release of pathogens from facilities used to keep harmful viruses in could lead to a natural disaster if the building wasn’t constructed as per the strict specification requirements.
So how does the process of constructing a clean room prevent any costly errors from being incorporated into it?
Planning, planning, planning! Cleanrooms take years to plan and the designs for these are agreed upon long before a piece of steel is installed, or a brick is laid. There is a strict process for cleanroom construction which is the Qualification Process. This process is made up of 4 stages and these should be followed strictly with work not being allowed to move to the next stage until the one before it has been completed and validated by competent professionals experienced in this field of work.
The 4 stages are:
- Design Qualification – This is the first and most important stage in the whole process. In this stage, there will be a requirement to provide proof that the design of the cleanroom and all its component parts is compliant with regulatory requirements and the process needs. To ensure that no errors are allowed to pass this stage the designs are reviewed and approved to then allow materials and products to be procured for the cleanroom build.
- Installation Qualification – In this stage, the installation is checked to ensure that what was signed off at the design stage is exactly what was built on site. If the approved design drawing required 10 sockets to be installed in a room at a certain height and spacing centre, then this is what will be checked against to ensure that is what has been installed. Again, the purpose of this stage, like all of the others, is built on evidence to prove that the installation is compliant and confirms that the installed cleanroom is consistent with what was specified. There can be no deviation and those charged with doing the work are aware that this is the case.
- Operational Qualification – means showing it works as intended in all respects. This could be in the form of a door opening and closing, a ventilation
fan running or a piece of equipment operating. The evidence of this operational check is recorded to allow the process to move into the final step.
- Performance Qualification – As with all of the earlier steps, the proving of these items isn’t in the form of testing but relies on showing (which is a fundamental of auditing – you could argue that each stage of the qualification is audited before the next stage is allowed to progress with any corrective actions being rectified before moving on). This stage means showing that the cleanroom delivers the overall desired performance together in an operating state when integrated with all other elements of the build from air-locks, EMS (environmental monitoring systems), lighting and pressure cascade (either positive or negative).
No ‘product’ will be made or allowed to enter the cleanroom until the full qualification process has been completed and signed off as being GMP (Good manufacturing practice) compliant.
So, should the above method be utilised more in the wider construction industry? Absolutely!
There may be more cost upfront from getting a design freeze, however, the level of quality certainty at the end will be far higher than the current ‘self-certification’ process that is allowed to exist at present. It would also ensure that the customer’s requirements were achieved and that any legacy defects would be a thing of the past.