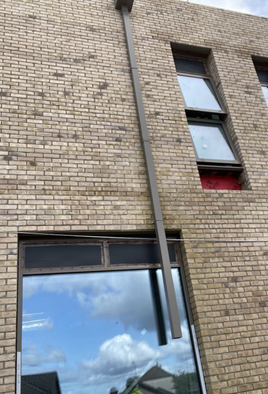
All too often the subject of quality is tagged on to the end of the agenda of a site progress meeting, usually alongside Health & Safety. At the end of a lengthy meeting it is invariably glossed over, with little to no real discussion, with perhaps a brief update on the numbers of snags and non-conformances on the quality tracker and how that has changed in the month.
One of the innovations that CQIC is encouraging is the use of a dedicated quality meeting. A meeting which will include –
- Agreeing the processes and procedures for each of the parties in their collaboration on quality and to monitor that they are working.
- Discussion of forthcoming work, the risks that are known for such work and what proactive measures are being taken to get the work right first time.
- Consideration of the Lessons Learned log which was jointly developed by the Client and the project team from their collective experience on previous projects (including from Post Project Reviews), and how these Lessons Learned are actually being used to avoid error.
- To review the quality records being captured and progress in rectifying snags, defects and non-conformances.
- To identify areas of concern on quality and to discuss what actions are being taken to address them.
- To hear what errors have occurred in the last period, why did the errors occur and what is being done to avoid them happening again.
- What work is being done on benchmarking and samples.
- To provide an opportunity for formal liaison between the Client’s quality monitors and the contractor.
- To receive a report on areas such as Building Standards and Manufacturers / 3rd Party Tests and Inspections.
Fundamentally, the quality meeting keeps the subject of quality to the fore and ensures that collaboration on the subject is effective.
The subject of quality meetings came up in recent discussions with a procuring authority. They had included in their quality plan that they would be holding one. 6 months into the construction and no quality meeting had been held. They had been meaning to discuss the setting up of a quality meeting at the progress meeting, under the agenda heading of “Quality”, but time always seemed to run out. Their observation was that quality seemed to be going OK so, did they really need a separate meeting to actually discuss it.
The problem with quality is that it is always going fine… until it is not. No project sets out to have quality failures. It always just seems to happen. The quality meeting is an opportunity to be pro-active in the delivery of quality, to catch things before they become issues and to give the subject the priority and focus it requires and deserves. The recommendation to that authority was don’t wait until quality starts to go wrong until you discuss it – hold a quality meeting. It could be the most valuable hour of the month in terms of the outcome of the project.